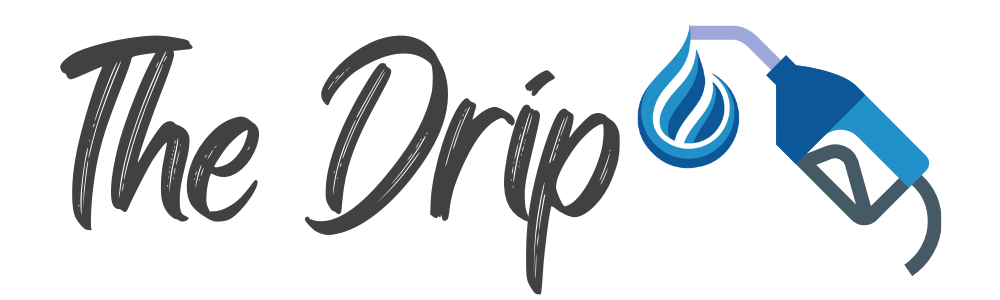
Mechanical line leak detectors have been an essential tool in the oil and gas industry for decades. These devices are used to detect and locate leaks in pipelines and other mechanical systems, helping to prevent costly damage and environmental hazards.
The history of mechanical line leak detectors can be traced back to the early 1900s, when engineers first began experimenting with different methods for detecting leaks in pipelines. Early detectors were simple and crude, often relying on visual inspections or the use of soap bubbles to locate leaks.

As technology advanced, mechanical line leak detectors became more sophisticated and accurate. Today, state-of-the-art detectors use a variety of methods, including ultrasonic, pressure, and temperature sensors, to detect even the smallest leaks in pipelines.
One of the most innovative mechanical line leak detectors on the market today is the product by Vaporless Manufacturing. This company offers the only mechanical line leak detector with an integrated check valve, making it an even more effective and reliable tool for detecting leaks.
Federal regulations require the use of mechanical line leak detectors:
There are several federal regulations that require the use of mechanical line leak detectors in the oil and gas industry. Some of the main regulations include:
- The Pipeline Safety, Regulatory Certainty, and Job Creation Act of 2011, which requires operators of certain pipelines to implement leak detection systems.
- The Oil Pollution Act of 1990, which requires operators of oil pipelines to have emergency response plans in place, including the use of leak detection systems.
- The Clean Air Act, which regulates the release of certain pollutants, including methane, and requires operators of certain facilities to implement leak detection and repair programs.
Additionally, the U.S. Department of Transportation's Pipeline and Hazardous Materials Safety Administration (PHMSA) has regulations in place that require operators of gas pipelines to have a leak detection program in place, and operators of hazardous liquid pipelines to have a method for identifying and evaluating leaks.
New York State and Line Leak Detection:
The New York State Department of Environmental Conservation (NYSDEC) has regulations in place that require operators of oil and gas pipelines to have emergency response plans in place, including the use of leak detection systems, to prevent and respond to spills and leaks. Additionally, the NYSDEC also has regulations in place that require operators of certain facilities to implement leak detection and repair programs to reduce the release of certain pollutants, including methane.
It is also worth noting that the state of New York has a strong commitment to reduce greenhouse gas emissions and to promote clean energy, which might also require the use of leak detection systems to reduce the release of methane and other pollutants, as well as to meet the state's emissions reduction targets.
OMNTEC acquires VMI
In 2022, Vaporless Manufacturing was acquired by OMNTEC Manufacturing, a Ronkonkoma, NY based company, further expanding the company's capabilities and reach in the industry. With the combination of their cutting-edge technology and OMNTEC’s expertise in manufacturing ATGs, Vaporless is poised to continue to be a leader in the field of mechanical line leak detection.
Overall, the history of mechanical line leak detectors is one of constant innovation and improvement. With companies like Vaporless Manufacturing and OMNTEC Manufacturing leading the way, the future of mechanical line leak detection looks bright.
Related OMNTEC Products:
Relevant Keywords: mechanical line leak detector, oil and gas industry, pipelines, ultrasonic, pressure, temperature sensors, Vaporless Manufacturing, OMNTEC Manufacturing, check valve, leak detection, Ronkonkoma, NY, innovation, improvement